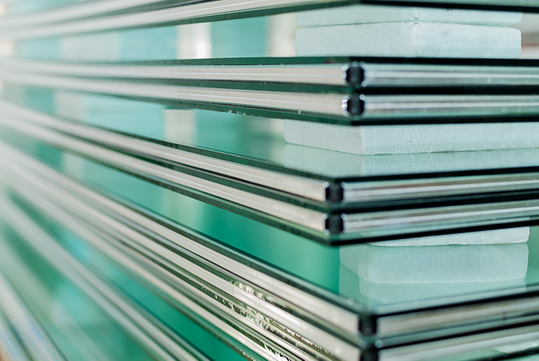
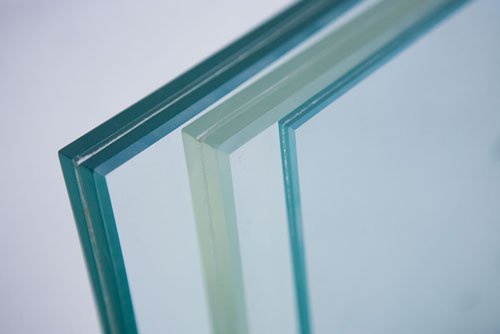
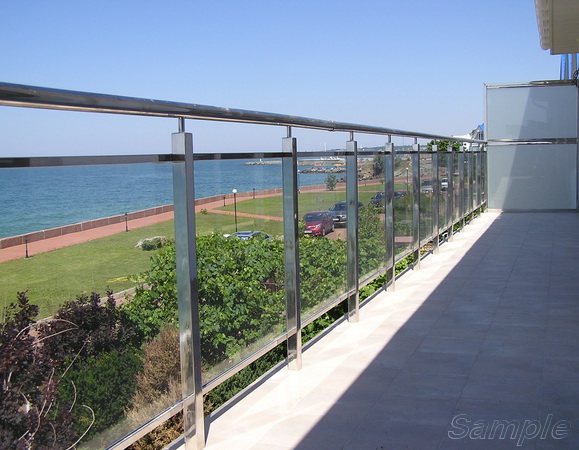
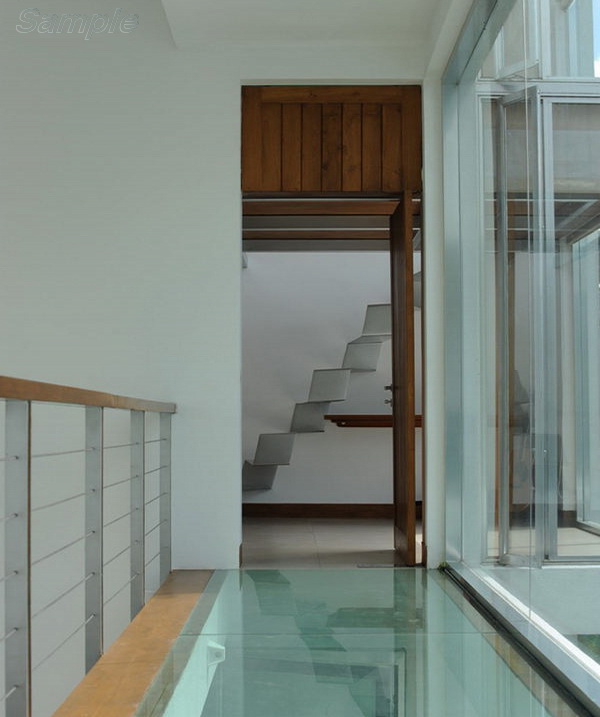
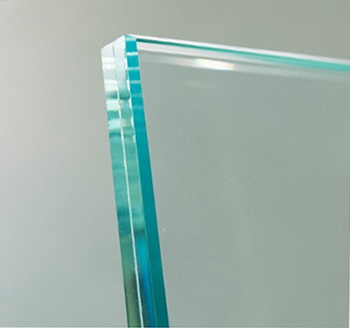
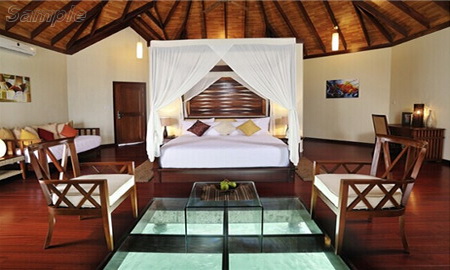
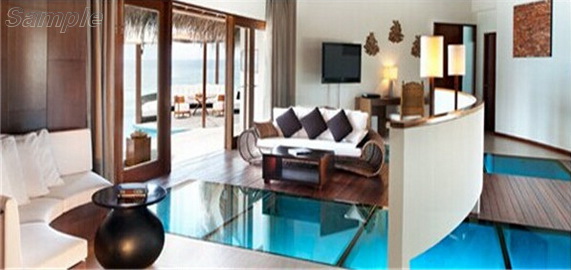
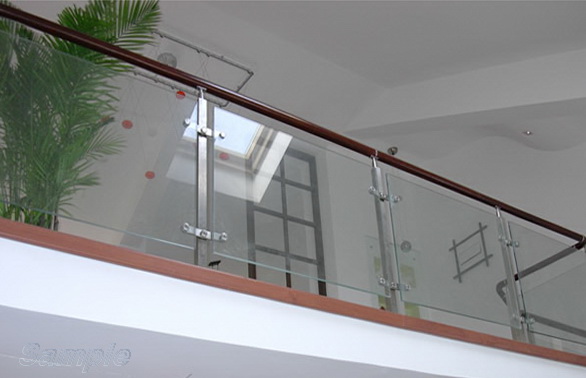
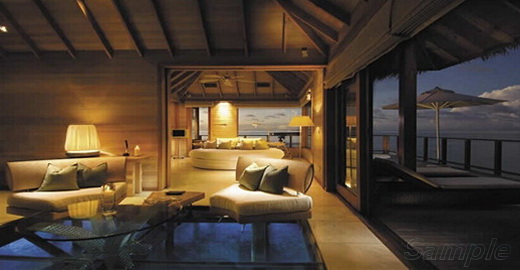
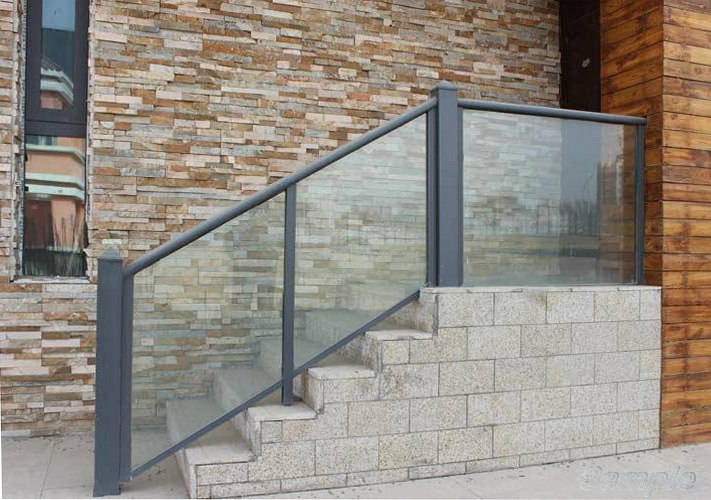
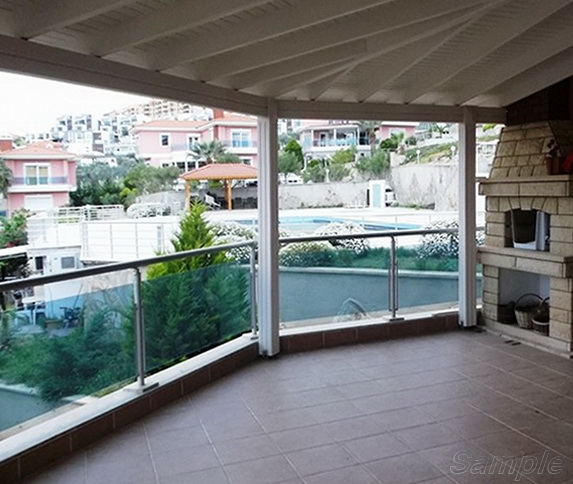
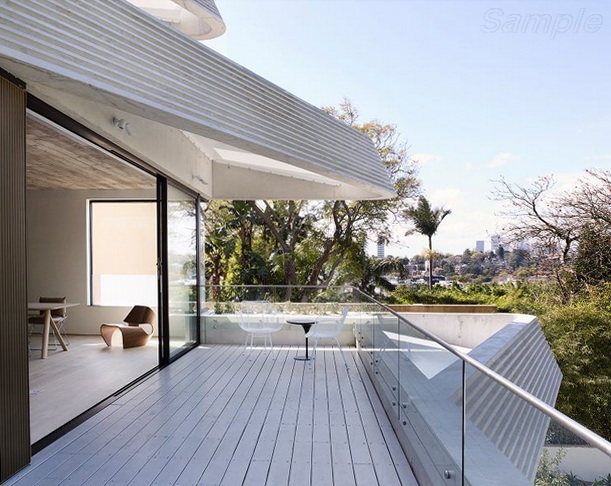
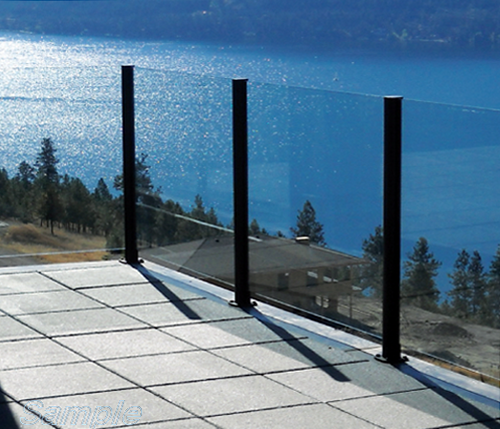
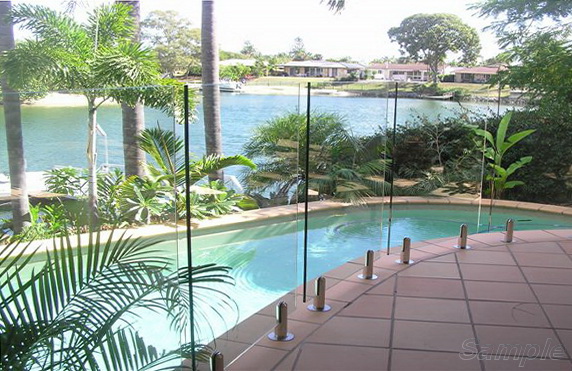
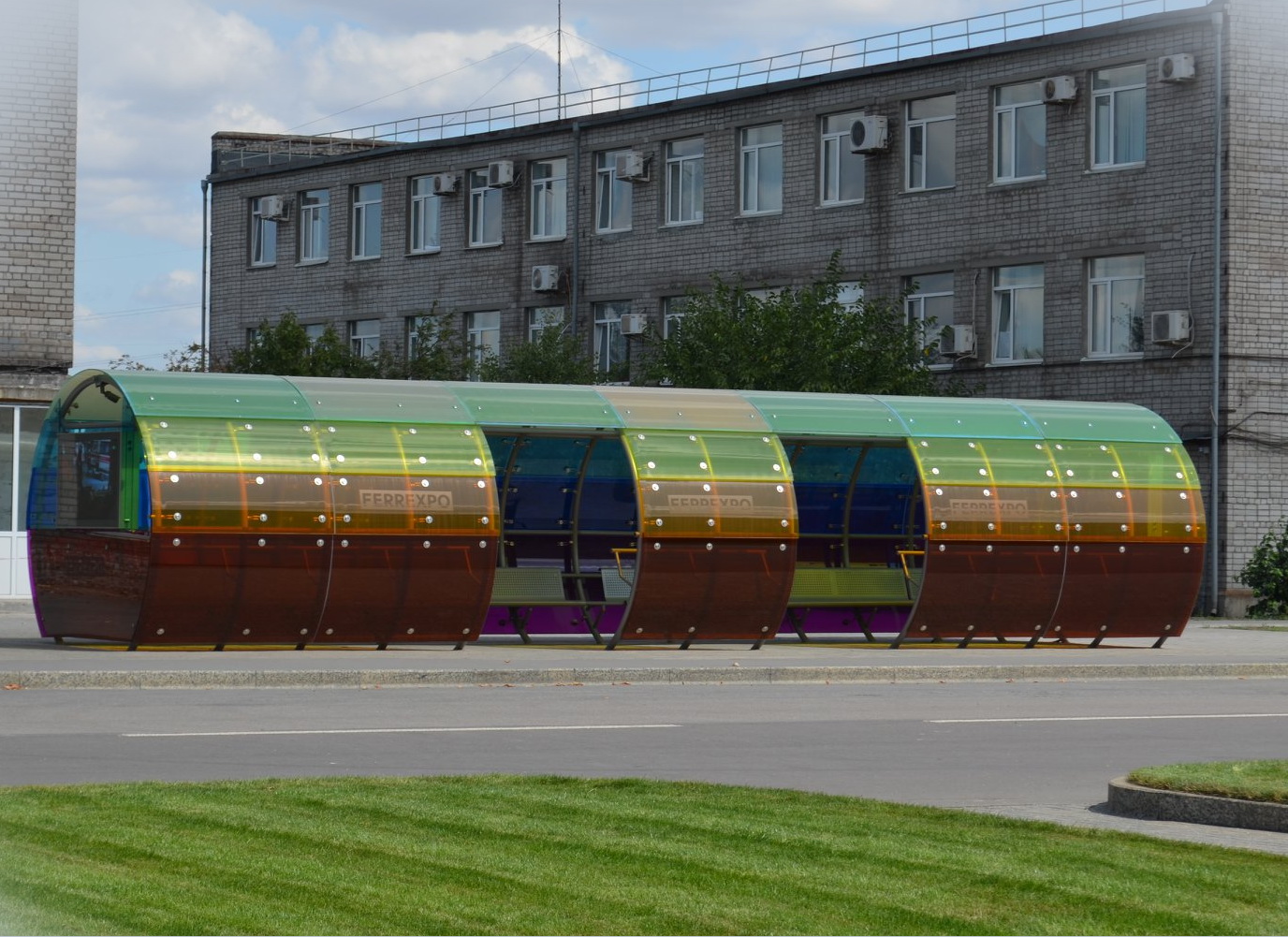
Ламіноване скло – блискуче поєднання функціональності і безпеки
Ламінованим багатошаровим безпечним склом триплекс (VSG – Verbundsicherheitsglas /De/, Laminated safety glass /En/) називають листові скляні вироби, що складаються з декількох шарів скла і сполучного полімерного матеріалу, з’єднаних один з одним по всій площині. Таке скло відноситься до класу безпечних, оскільки здатне залишатися в отворі навіть після руйнування і утримувати на плівці утворилися осколки. “Триплекс” може складатися з однакових, або різних по товщині, типу і призначенню скла і полімерних шарів. Підсумкова товщина отриманого виробу залежить від кількості скла і шарів полімерів в його складі і їх товщини. “Триплекс” виробляється як у вигляді пласких, так і у вигляді гнутих скляних виробів.
Історія створення триплекса
У 1903 році французький хімік Едуард Бенедиктус в процесі проведення одного зі своїх експериментів впустив скляну колбу на підлогу. Після падіння посудину тріснув, але не розпався на осколки, зберігши свою початкову форму. Цей факт викликав подив ученого, який вирішив проаналізувати таку незвичайну ситуацію. Як виявилося, раніше в цій колбі знаходився ефірно-спиртовий розчин нітрату целюлози. Випарувавшись, суміш залишила на стінках тонкий невидимий шар нітрату целюлози, який після падіння і утримував фрагменти скляної колби.
Слід згадати, що в автомобілях тих часів використовували звичайне скло, яке в разі аварії розбивалося на безліч гострих небезпечних уламків і моглио травмувати водіїв і пасажирів. Ставши свідком однієї з таких аварій, Едуард Бенедиктус згадав про колбу, в його лабораторії, яка впала, але зберегла свою форму. Після серії експериментів, він виготовив першу подобу «Ламінованого скла» , яке складалося з двох стекол, з’єднаних між собою шаром нітрату целюлози. У 1909 році Бенедиктус отримує патент (French patent 405, 881) на безпечне скло, яке він назвав «триплекс» (Triplex) і заснував фірму Société du Verre Triplex.
Через високу вартість ламінованого скла, автовиробники тих років не поспішали застосовувати його для скління автомобілів. У той же час, “триплекс” викликав інтерес у виробників військової техніки і знайшов застосування під час I Світової війни, як скло для військових автомобілів, літаків і окулярів протигазів.
Варто зауважити, що були і альтернативні розробки методу Бенедіктуса. Так, наприклад, в 1905 році англієць Джон Вуд розробив і запатентував подібний вид безпечного скла. В якості поєднюючого шару він запропонував використовувати натуральний каучук, що було досить дорого, та й прозорість скла залишала бажати кращого. З цих причин його розробка не вийшла в масове виробництво. C 1919 року заводи Форда почали використовувати ламіноване скло для лобового скла своїх автомобілів, а вже в 1929 році такий стандарт був введений для всіх моделей Форд. Надалі, за його прикладом пішло більшість інших автовиробників.
Технології виробництва скла триплекс
Для виготовлення багатошарового скла в даний час використовують 3 основні технології, які впливають на підсумкові властивості виробів:
- рідинне ламінування
- автоклавного плівкове ламінування
- безавтоклавні плівкове ламінування
Рідинне ламінування
Процес виготовлення рідинноламінованого скла починається з підготовчої стадії: скло ріжуть, шліфують краї і очищають.
По периметру листа скла закріплюють бутиловий стрічку, зміцнену ниткою зі скловолокна або PVC, в якій залишають невеликий проміжок для подальшого заповнення смолою і видалення повітря. Підготовлене скло з бутиловой стрічкою накривають другим склом того ж розміру. Потім скляні пластини здавлюють, щоб бутилова стрічка розпливлася на задану товщину. Потім, зібрану заготівку встановлюють в похиле положення під кутом близько 70-80 градусів.
Рідиннобразна смола, дозована відповідно до обсягу проміжного простору, заливається всередину склопакета. При розрахунку необхідної для заповнення кількості враховують величину усадки смоли, зазначену її виробником. Коли в проміжний простір влито точно розраховану кількість смоли, склопакет повертають в горизонтальне положення. Ламінуючу рідину, рівномірно розподіляють, стискаючи роздуту центральну частину заготівки. Після видалення залишків повітря і надлишків смоли з склопакета, отвір закривають бутиловою стрічкою. Тужавіння відбувається в горизонтальному положенні.
Смоли, з точки зору полімеризації, можна розділити на дві групи. Одну групу утворюють смоли, в яких каталізатори, перемішані з основною речовиною, забезпечують процес полімеризації. Полімеризація такої смоли – це екзотермічна хімічна реакція, при якій виділяється тепло. Час затвердіння залежить від температури – чим вище температура, тим коротше час затвердіння. Наприклад, затвердіння шару смоли товщиною в 1 мм при температурі 20 ° С триває близько 2,5 годин, а при температурі 30 ° С – близько 1,5 годин.
В іншу групу входять однокомпонентні смоли, що тверднуть під впливом ультрафіолетового випромінювання. Під час реакції, при якій відбувається затвердіння, тепло не виділяється, а полімеризація під УФ лампою призводить до затвердіння протягом 10-25 хвилин.
Рідинне ламінування є єдиною технологією яка не передбачає використання підвищених температур. Виготовляти кольорове скло можна шляхом додавання пігментів в рідину для ламінування.
Недоліки “заливного” триплекса (рідинного ламінування):
- застаріла і екологічно небезпечна технологія;
- неможливість використання декоративних вставок;
- потрібно додаткове очищення торців від залишків смоли і бутиловой стрічки;
- в готовому виробі під впливом сонячного УФ випромінювання може тривати процес полімеризації, що призводить до надмірного затвердіння і подальшого розтріскування смоли;
- більше візуальних дефектів порівняно з плівковим триплексом, різна товщина;
- коротший термін експлуатації виробу.
Автоклавне плівкове ламінування скла (плівка PVB)
Автоклавне плівкове ламінування скла є традиційною і найбільш поширеною на сьогоднішній день технологією виробництва триплексу. Як і інші технології плівкового ламінування, вона заснована на принципі повітронепроникного з’єднання плівки і скла. Плівка PVB (PolyVinyl Butyral / полівініл Бутірал) – основний вид ламинуючої плівки використовуваної для автоклавного ламінування.
Автоклавний метод ламінування дозволяє здійснювати збірку багатошарового скла в його остаточних розмірах і формі (наприклад, автомобільне лобове скло), а також виробляти листи великих розмірів, в тому числі стандартних заводських PLF або т.зв. “Jumbo” розмірів 6000×3210 мм, з яких в подальшому вирізають вироби необхідних габаритів.
Виробництво багатошарового скла автоклавним методом здійснюється в кілька етапів і в значній мірі може бути автоматизовано. Перед розміщенням між скляними заготівками полімерної плівки PVB, скло, в обов’язковому порядку ретельно миється і знежирюється. Якщо в складі виробу використовується більше двох шарів скла або хоча-б одне скло загартоване, перед ламінуванням їм надають остаточний розмір і форму, виробляють всі необхідні вирізи і отвори. Після процесу складання наступний етап-це попереднє ламінування – двостадійне стиснення скляних елементів. Перша стадія – це так звана «холодна правка» – пресування в роликовій машині, після чого пакет (триплекс) нагрівають до 80-90 ° С – стадія «гарячої правки». Далі виріб переміщують в автоклав, де за допомогою комбінації теплового впливу – температура 150 ° С і тиску 12.5 Бар в автоматичному режимі і відбувається остаточне опресування багатошарового ламінованого скла.
Недоліки автоклавного плівкового ламінування на основі PVB плівки:
- Висока вартість обладнання, що позначається на собівартості виробів;
- Необхідність герметизації торців триплекса для зменшення ризиків деламінаціі. Оскільки PVB плівка вразлива до підвищеної вологості, розшарування вироби експлуатованого у вологих або екстер’єрних умовах може відбутися протягом декількох років;
- Деламінація може відбуватися також і в місцях вирізів і отворів для установки фурнітури;
- Розшарування автоклавного триплекса можуть викликати значні статичні навантаження при знижених або підвищених температурах;
- Практично відсутня можливість використання декоративних вставок, через низьку адгезії PVB плівки до скла і практично нульовий адгезії до більшості інших матеріалів.
Безавтоклавні плівкове ламінування скла (плівка EVA) – триплекс від ГлассПро
ламинирования закладка перемещается в печь и подключается к вакуумному насосу.
Компанія ГлассПро використовує одну з найбільш сучасних технологій – безавтоклавне вакуумне ламінування на основі EVA (EthilenVinilAcetat / Етиленвінілацетат) плівки, яка дозволяє виробляти найбільш якісне і довговічне багатошарове ламіноване скло – триплекс.
Дана технологія набуває стрімку популярність у всьому світі і також, як і інші технології плівкового ламінування, заснована на герметичному з’єднанні між собою плівки та скла.
Основною відмінністю від автоклавного ламінування є використання більш сучасного полімерного складу EVA плівки, завдяки якому для отримання високоякісного готового продукту відпадає необхідність використання автоклава в виробничому циклі. Технологія виробництва безавтоклавного вакуумного плівкового ламінованого скла, як і в випадку з автоклавною, ділиться на кілька стадій: підготовка пакету і його спікання.
Підготовка пакету:
- Скло ріжеться в розмір готових виробів, обробляється край;
- У разі застосування в складі триплекса загартованого скла, йому спочатку в обов’язковому порядку, надається остаточний розмір і форма, проводяться всі необхідні отвори і вирізи, і здійснюється гарт заготовок;
- Скляні заготовки миються в спеціальній професійній мийній машині з використанням демінералізованої води очищеної системою зворотного осмосу і потім додатково обезжирюються;
- EVA плівка для ламінування нарізається в необхідних для пакета розмірах;
- На скло укладається ЕтіленВінілАцетатна полімерна плівка і накривається наступним склом (можливо різна кількість шарів, використання декоративних або армуючих вставок);
- Перед переміщенням заготовки в піч для ламінування, пакет упаковується в герметичний силіконовий конверт (мішок), забезпечений спеціальним штуцером для його підключення до вакуумного насоса;
- Зібрана для ламінування закладка переміщається в піч і підключається до вакуумного насоса.
Вакуумне ламінування – відбувається в кілька етапів, на професійному жаргоні званих «полками». Кожна «полиця» або етап ламінування характеризується трьома параметрами: тривалістю, температурою і ступенем вакууму. Параметри «полиць» змінюються в залежності від кількості, товщини і типів скла, що входять до складу триплексу, параметрів EVA плівки і ряду інших чинників. Отримати якісний виріб можливо тільки в разі підбору правильних параметрів і їх чіткого відстеження в процесі ламінування. Компанія ГлассПро володіє сучасним виробничим обладнанням, де весь процес виробництва багатошарового скла контролюється комп’ютерним управлінням.
- Холодний вакуум – ця стадія передбачає створення розрідження в робочій зоні за допомогою вакуумного насоса з метою видалення залишків повітря і попереднього формування заготовки. Зазвичай, витримка заготовки на цій фазі становить 15-20 хвилин без додаткового нагріву.
- Нагрівання – в цій фазі при збереженні розрідження близько “- 1,00” бар здійснюється нагрів заготовки. Залежно від типів використовуваних плівок і додаткових декоративних вставок, температурний режим змінюється від 90 до 130 градусів Цельсія. Температура підбирається таким чином, щоб розм’якшити полімерну плівку в достатній мірі і забезпечити процес полімеризації молекул. Важливою умовою є рівномірний нагрів всієї поверхні виробу.
- Витримка – протягом цієї фази зберігається задана температура і розрідження. Тривалість стадії залежить від кількості і товщини скла у виробі і кількості шарів плівки.
- Охолодження – є завершальним етапом виробництва ламінованого скла. Здійснюється при збереженні розрядження «- 0,95» бар до падіння температури до 55 градусів Цельсія. Потім вакуумний насос відключається і подальше охолодження виробу відбувається в звичайному середовищі.
Переваги технології вакуумного ламінування на EVA плівці:
- Підвищена безпека виробництва, за рахунок відмови від роботи з високими температурами і тиском;
- Технологія є екологічно чистою;
- За рахунок високої адгезії EVA плівки до скла та інших матеріалів дозволяє застосовувати різні вставки з тканин, кольорових полімерних плівок, металу, каменю і т.д. для виготовлення декоративного триплекса;
- Можливість застосування в екстер’єрних умовах, завдяки високій стійкості до підвищеної вологості, перепадів температур, сонячної радіації та інших несприятливих факторів зовнішнього середовища.
Сфери застосування ламінованого скла
Скління будівель і споруд
- Фасадне скління
- Спайдерне скління
- Скляні покрівлі та дах
- Вікна
- Скло для огорож
- Скляні зупинки
- Скляні козирки і навіси
- Вітражні конструкції і вітрини
- Скляні вхідні групи
Інтер’єрне скління
- Скляні перегородки для житлових приміщень
- Скляні перегородки для офісних приміщень
- Мобільні скляні перегородки
- Скляні двері
- Скляні душові кабіни і огорожі
- Скляні меблеві фасади і кухонні фартухи зі скла
- Скляні столи, барні стійки і стільниці
- Скляні ступені (сходи)
- Скляні огорожі сходів (перила)
- Скляна підлога як елемент перекриття
- Фальшпідлога з скляних панелей
- Скління ліфтових шахт
- Скління спортивних об’єктів
Скління транспортних засобів
- Лобове скло для автотранспорту і авіації
- Скло для спецтранспорту та робочих машин
- Ілюмінатори космічних станцій
- Вікна та ілюмінатори кораблів
- Вікна для залізничного транспорту
Спеціальне застосування
Скло спеціального призначення, як правило, являють собою ламіноване скло складного складу. Це обумовлено високими вимогами до елементів скління робочих місць в банках, ювелірних і збройових магазинів, сховищ цінностей, постів охорони, стекол броньованих автомобілів.
- Куленепробивне скло
- Антивандальне скло
- Пожежо-, вибухостійке скло
- Звукоізолююче скло
- Захист від UV випромінювання
- Скло з регульованою прозорістю
- Скло для систем сонячної енергетики