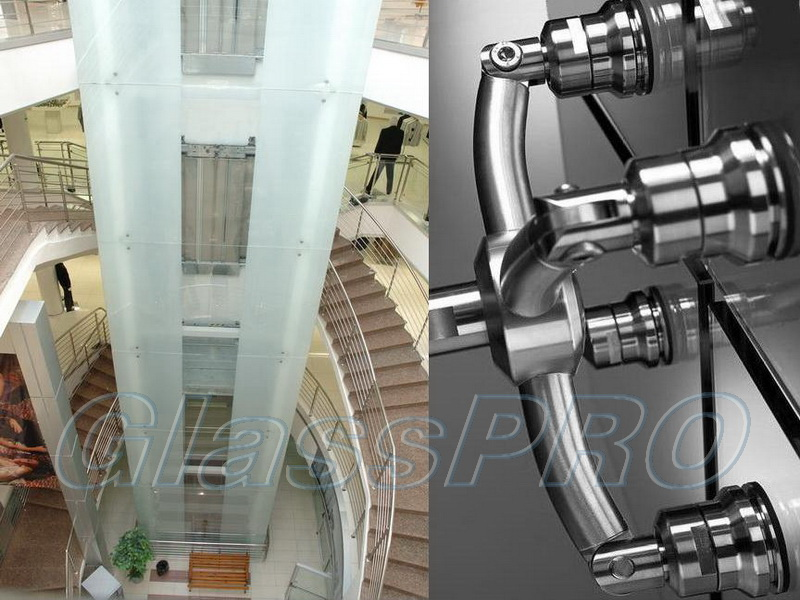
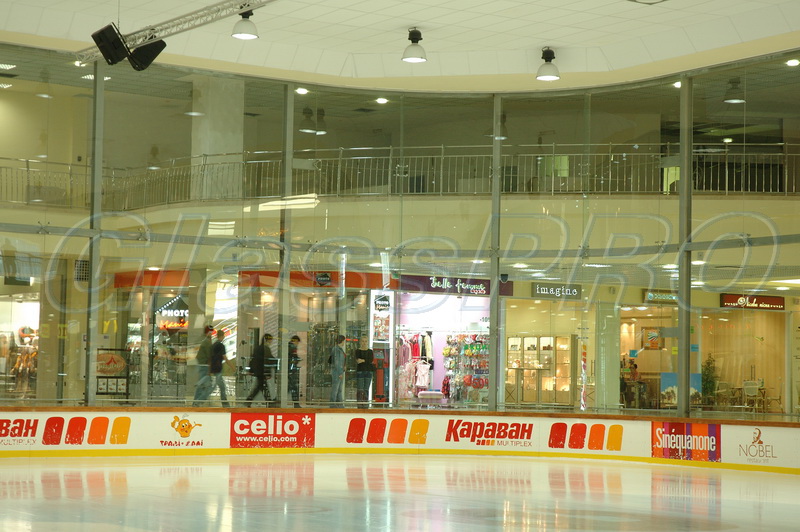
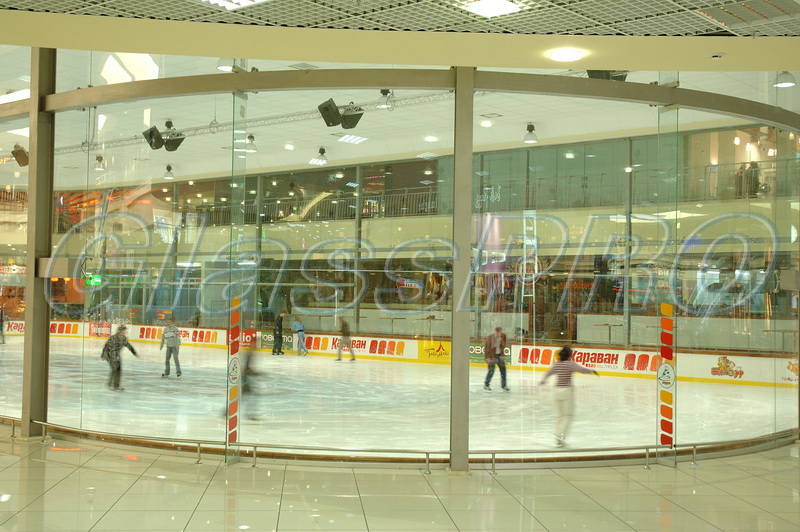
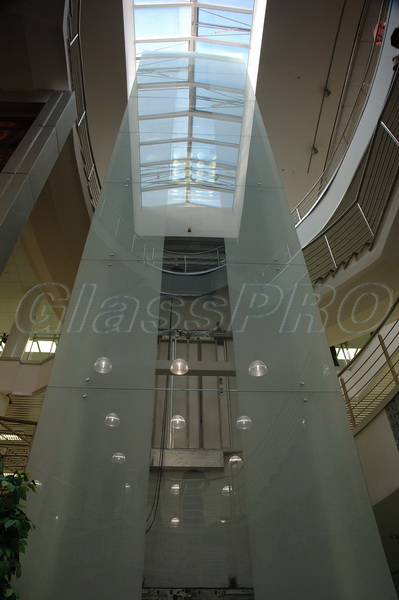
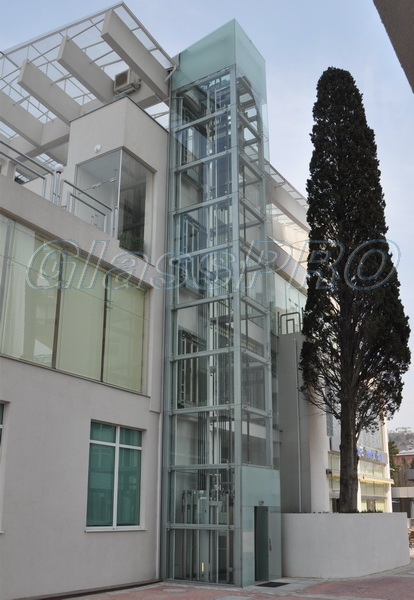
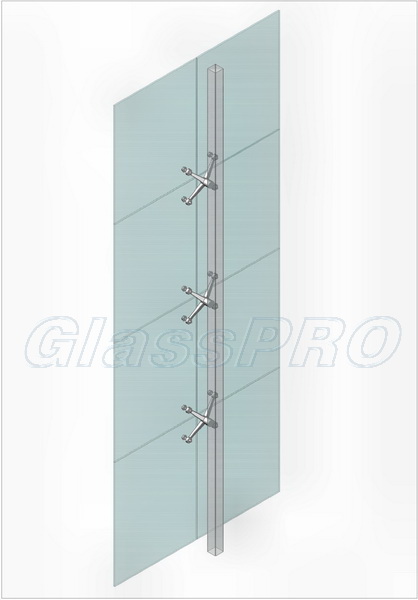
“Spider systems – high tech solutions of modern architecture!
A bit of history – in 1982, one of the global leaders in the production of building glass, the British company Pilkington, presented a fundamentally new system of Pilkington Planar™structural glazing. This cutting-edge technology , called «planar» glazing, stood out for its ability to create perfectly smooth monolithic glazed surfaces of various shapes and sizes, not dissected by window frames or metal profiles. The fastening of glass panels to the supporting structure was first executed by using point hinges recessed into conical holes in the glass. They were interconnected by beam spatial metal brackets called “spiders” (from the English word), giving the system an alternative name: “spider” glazing.
This move away from traditional frame glazing profiles ensured the durability and reliability of the new system, and simultaneously opened up additional possibilities for planning and design. The development of “spider” glazing has been a major step forward in urban architecture and has great potential. The minimum number of structural elements and maximum visual transparency allow you to create a unique futuristic architecture: a graceful aesthetic of the exterior and interior, an abundance of natural light, a sense of spaciousness, and a blurring of the line between the interior and the environment.
Where to use “spider” structures – the advantages of “spider” systems are most evident when glazing large-scale facades of buildings, where it is necessary to provide maximum visual access to the interior from the outside – such as in car dealerships, exhibitions, etc. In this respect, no other glazing system can compete with “spider” designs. When glazing recreational and leisure centers, swimming pools and winter gardens, another indisputable advantage of “planar” systems becomes obvious: the highest transmittance of natural light. An interesting application is the so-called “Dual Skin”, system, in which a “spider” glazing structure is installed over the existing facade, forming an additional sheath which significantly improves thermal insulation and changes the architectural appearance of the building. “Spider” glazing is also used in canopies and awnings, domes, atriums, elevator shafts, railings, noise-isolating screens, and interior partitions. Spider glazing has been used in glass domes over historical monuments, protecting them from adverse weather factors while maintaining an unobstructed view. Glass panels can be configured in a variety of shapes and can be positioned at different horizontal and vertical angles to create stepped and curved glass structures.
How spider glazing works –along with aesthetic appeal and openwork design, “spider” glazing is very durable and has the ability to withstand various loads. Such loads are formed by the glass’s own weight, positive and negative wind pressure, the weight of snow on the inclined planes of the glazing, and thermal deformations of the structure. The structure of the “spider” facade is not absolutely rigid and allows the glass to bend under the influence of loads. The use of hinged fasteners helps to evenly distribute such loads along the attachment points, granting elasticity and resilience. It also compensates for possible static, dynamic and temperature stresses and transfers part of them to the supporting elements of the structure. This feature of “spider” structures prevents cracking and glass breakage.
Glass for “spider” systems – most types of modern glass can be used for “spider” systems, as well as specially configured glass units when demanded by increased thermal resistance, noise insulation or other functional requirements. It is mandatory that the selected glass is tempered, and often it is additionally laminated with other tempered or heat-strengthened glass. The most important criterion is safety, quality and geometric precision in the manufacture of glass elements. Read more about glass for “spider” structures…
Sealants in “spider” glazing – during installation, the joints between adjacent glass pieces are filled with special sealants. In exterior glazing, sealants have to fit special requirements to protect against the elements. They must have a high degree of fixation and adhesion to glass, be resistant to ultraviolet rays, and ensure reliable waterproofing and airtightness of the structure. In a wide range of temperatures, including low temperatures in the cold season, they must maintain the elasticity necessary to compensate for the thermal and dynamic deformations of the structure. LLC “GlassPro“ uses sealants certified for the conditions of Ukraine produced by “Sika“ (Switzerland) and “Dow Corning“ (USA). Additional polymer inserts are used to seal the joints between glass units. In addition to choosing the right type of sealant, quality assembly is required: the joint must be filled tightly and consistently.
Hinges for “spider” glazing (other name: grenades or ratulas) – provide the fastening of the glass panel to the beam bracket. Moreover, such a connection retains a certain degree of glass mobility relative to the hinge axis. Since various models of hinges differ in the value of the permissible load and the parameter of the maximum permissible angle of deviation from the central position of the axis (from ± 5 ° to ± 10 °), when choosing a hinge it is necessary to consider the specifics of a particular project, the type and size of glazing elements, and wind and snow-related stresses for the region. Based on these parameters, the maximum design values of glass deflection are calculated, which in turn allows you to select a hinge of the appropriate capacity with the required range of rod travel. There are models of hinges with a deflection angle of up to ± 20 °, which make it possible to install glass elements at an angle to each other during installation of complex facades. The hinges for spider glazing are made of the highest-quality stainless steel. Grade 316 is used for external glazing structures and rooms with high humidity which has special anti-corrosion properties. Grade 304 is used for interior applications.
Options for attaching hinges to glass panels and glass units in “spider” glazing:
The fixation of the hinges of the point fixings in the glass panels is executed by creating holes. The type of opening in the glass is determined by the hinge model. For some, simple cylindrical holes are used. The fastening then includes discs of a larger diameter, exceeding the size of the opening and protruding above the glass surface on the outside of the facade. Other models of hinges involve the use of conical holes, obtained by countersinking or, when using laminated glass, holes in the form of a complex different-sized cylinder. In this case, the outer part of the mount is recessed into the glass body, which results in an absolutely smooth glazing surface without protruding parts. Such designs have a more elegant appearance and are more convenient to use, since they do not have protruding parts that accumulate dirt and make it difficult to clean the glass. The most appealing option, which can only be achieved when using laminated glass or double-glazed windows, is the complete absence of the metal parts of the fastener coming out to the outer surface of the glass, when all the supporting parts of the fastening are fully integrated into the inner layers of the glazing element. Apart from the aesthetic advantages, this solution minimizes the risks of freezing and moisture condensation on metal structural elements inside the building. Since a high load concentration occurs when using point mounts in the places where the glass rests on the fastening part of the hinge, the hinge must include additional alignment rings made of soft high-purity (99.5%) aluminum of the EN AW-1050A type or polymer materials, excluding direct contact of glass with steel.
Brackets for “spider” glazing – serve to connect the hinges to each other and ensure the attachment of such a unit to the supporting structure. The model and parameters of the bracket are determined by the type of the bearing subsystem and the value of the design loads that it must withstand. Most of the manufactured bracket models are designed for radial loads in the range of 1000-2500 N for forces acting parallel to the glass plane caused by its weight, and 2000-6500 N for axial loads perpendicular to the glass plane (forward and reverse wind loads). The brackets are made of high-alloy stainless steel AISI 316 or special alloys based on aluminum such as Al Si 5 mg. In this case, the finishing surface of steel can be polished or matte (brushed), aluminum – anodized, or have a powder polymer coating of the PVF2 type in the colors of the RAL palette. Also, the company “GlassPro” provides the architect of the project with the opportunity to choose the design of the brackets among the options supplied by various manufacturers.
Multiple brackets for “spider” systems are installed in sets. The location of the “spider” fastener in the structure (in the field / along the edge / in the corner) determines the number of beams for attaching the hinges – usually from 1 to 4. In addition, the arms of the bracket differ in the type of fastening of the hinge: fixed or movable in one or all directions of the glazing plane. When designing a structure, it is important not only to use brackets of appropriate power, but also to properly select the configuration of the “spider,” taking into account the beam types.
Advantages of spider glazing systems:
- give maximum transparency and visual lightness to the entire structure by minimizing the number of additional supporting elements;
- provide smoothness of the glazing surface on both sides – exterior and interior;
- have durability and resistance to various weather conditions due to the use of glass and stainless steel, as the most inert materials that are not subject to corrosion and UV radiation;
- thanks to the sectional structure, in the event of damage to a separate glass element, simple and quick replacement is possible;
- easy to care for and require minimal maintenance costs.
Mounting layouts and substructures for “spider” glazing – the “spiders” of spider glazing, in turn, can be attached to the elements of capital supporting structures, to additionally constructed metal columns and cross bars, and can even give the impression of being suspended in the air, being fixed with cable-stayed trusses or supporting glass fins. The choice of system depends on the project budget, existing capital structures, and the architectural preferences of the client and architect.
Type of structure or installation | System types | |||
On load-bearing capital structures | On metal racks and structures | On glass fins | On a cable-stayed system | |
Facade glazing | + | + | + | + |
Inclined facade glazing | + | + | + | – |
Dual Skin | – | + | – | + |
Glass roofs, domes | + | + | + | + |
Elevator shafts | + | + | + | – |
Glass fencing | – | + | + | + |
Glass canopies | – | + | + | – |
Glass overhangs | – | + | + | – |
Glass vestibules | – | + | + | – |
Freestanding pavilions | – | + | – | – |