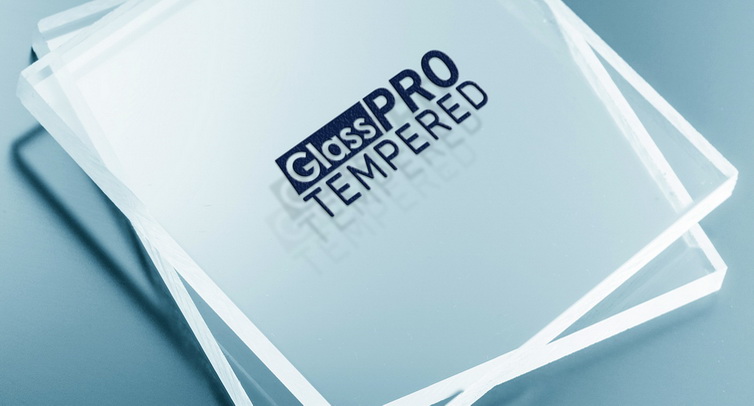
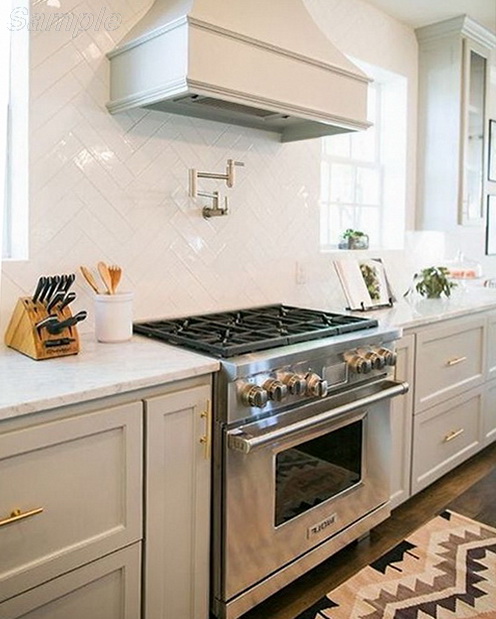
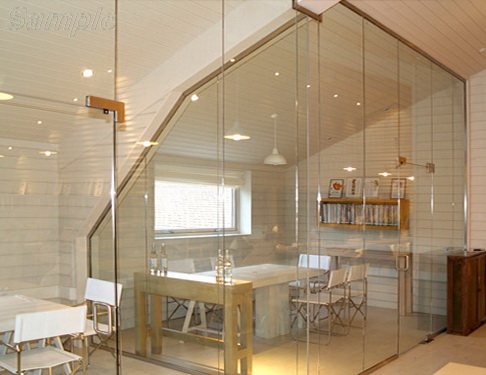
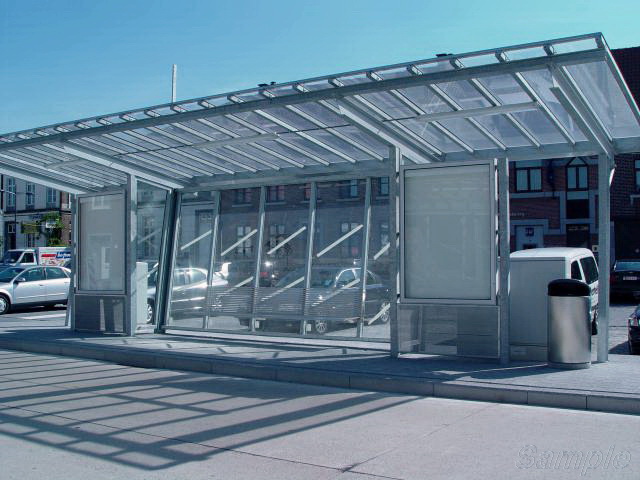
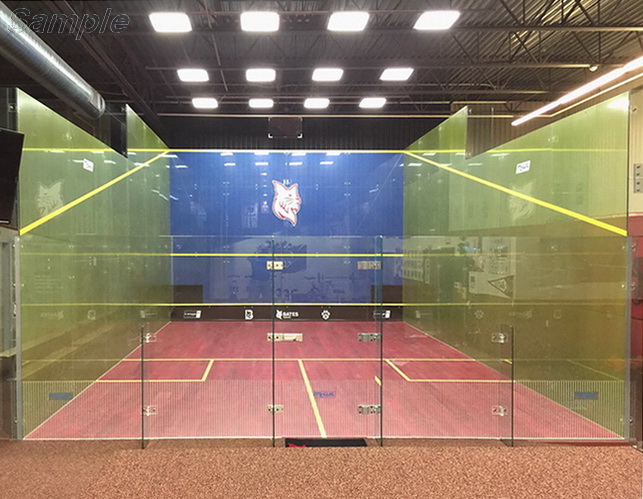
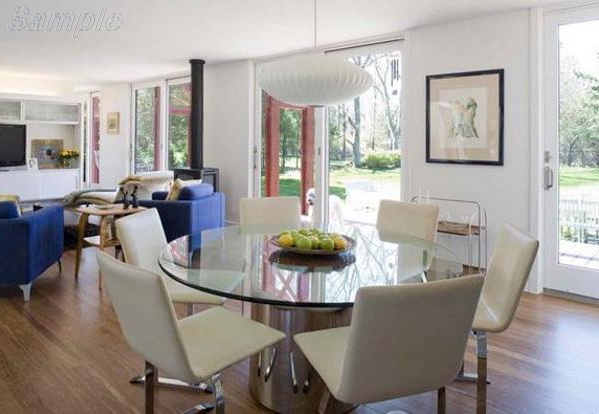
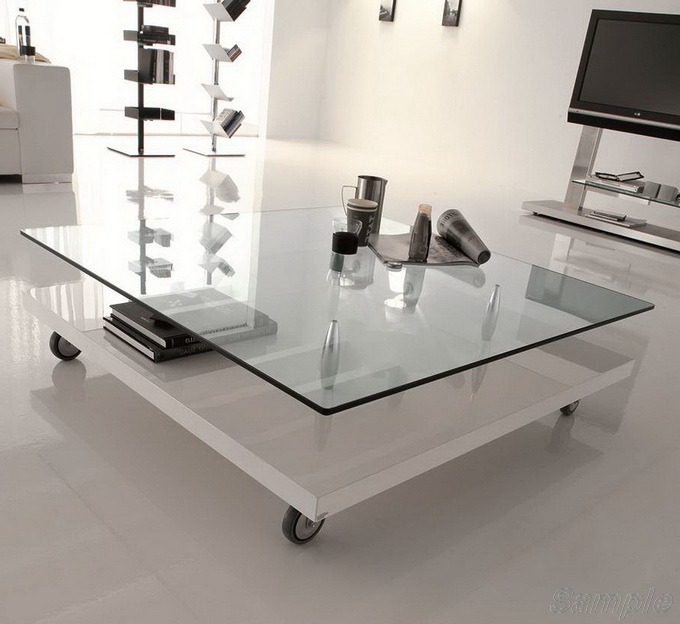
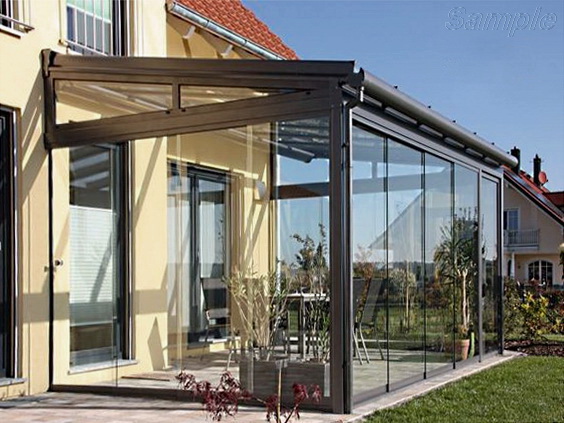
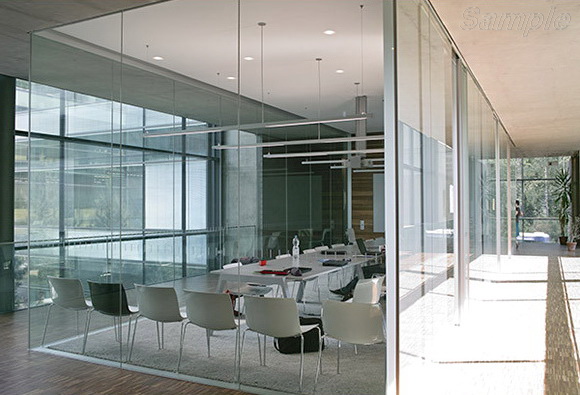
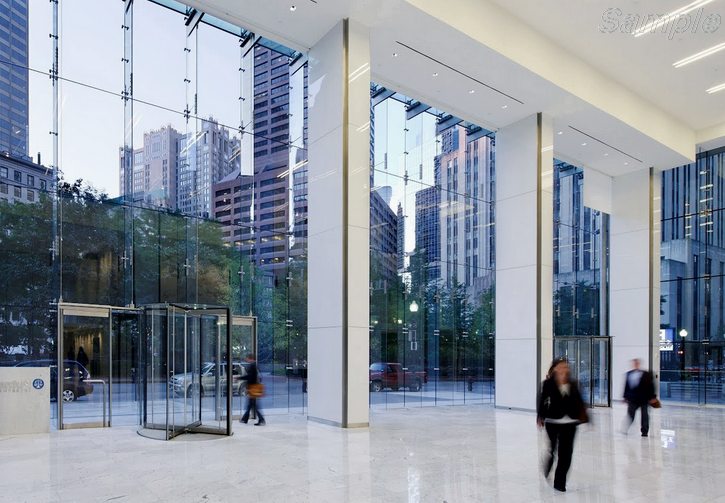
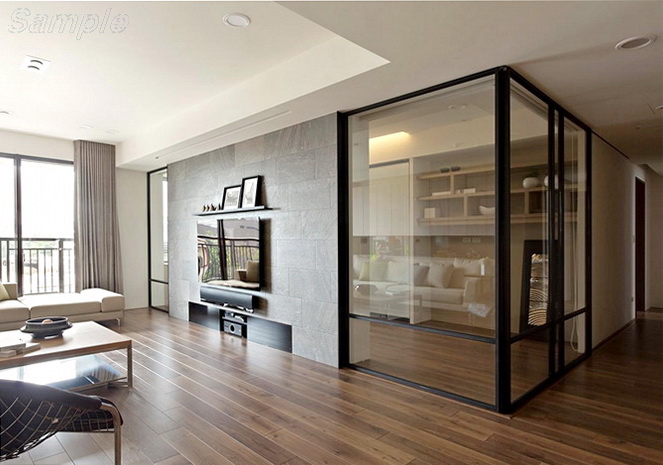
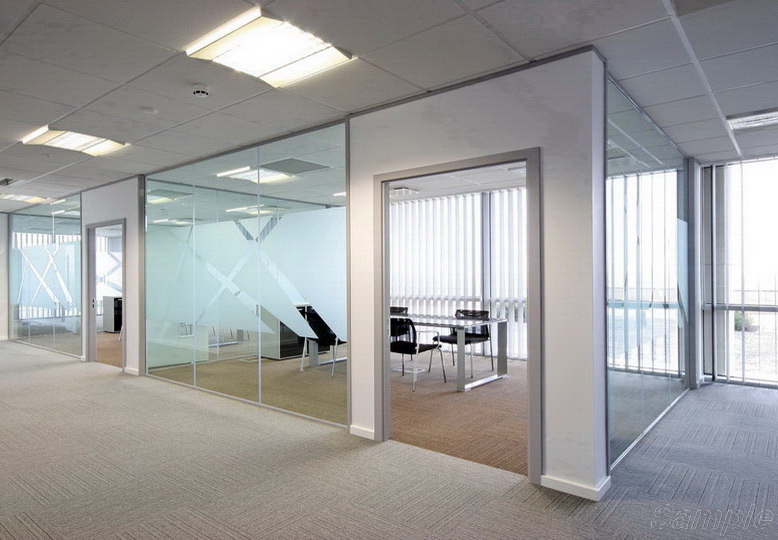
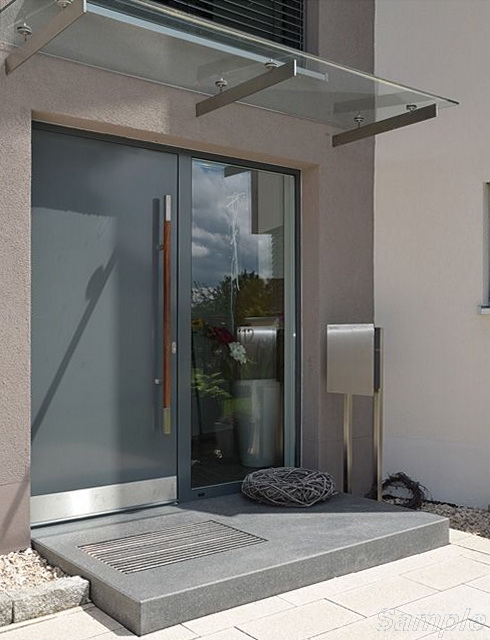
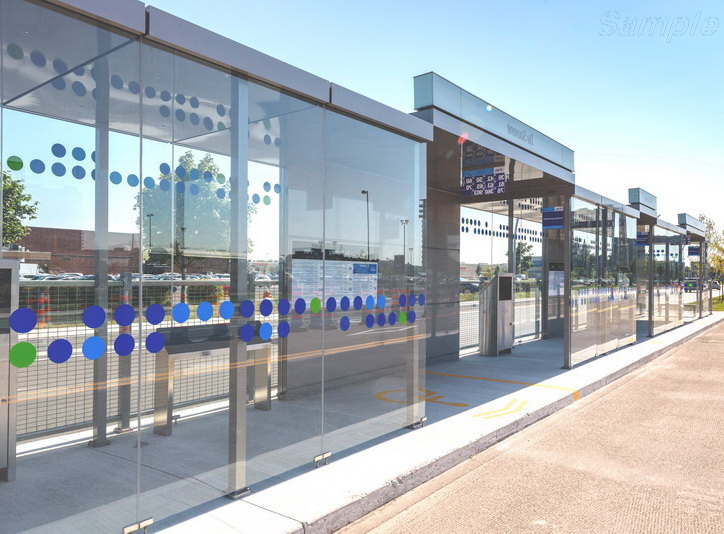
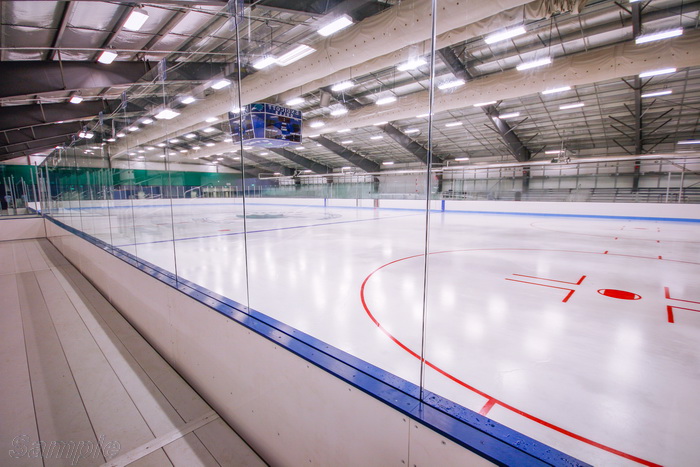
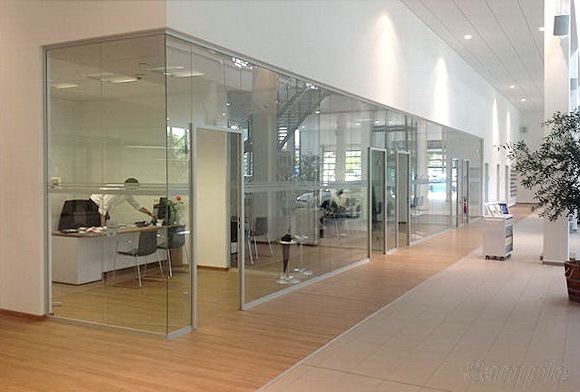
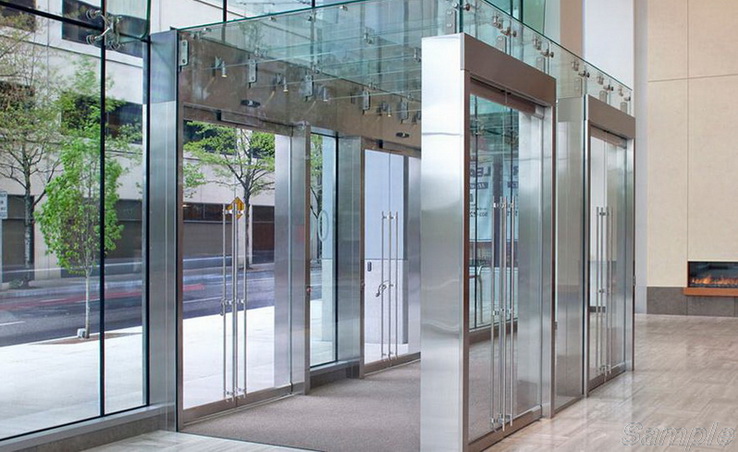
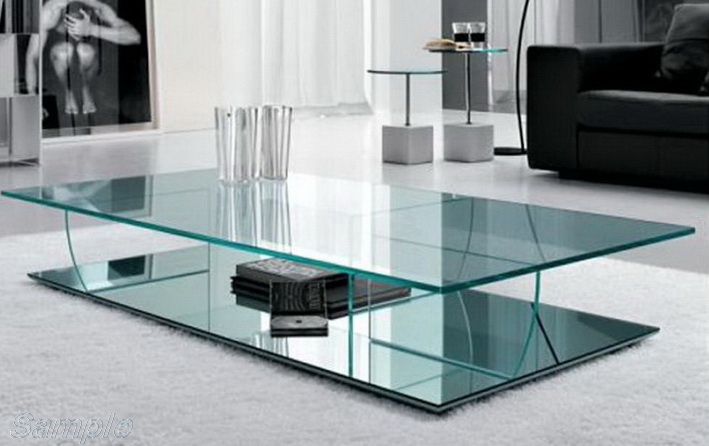
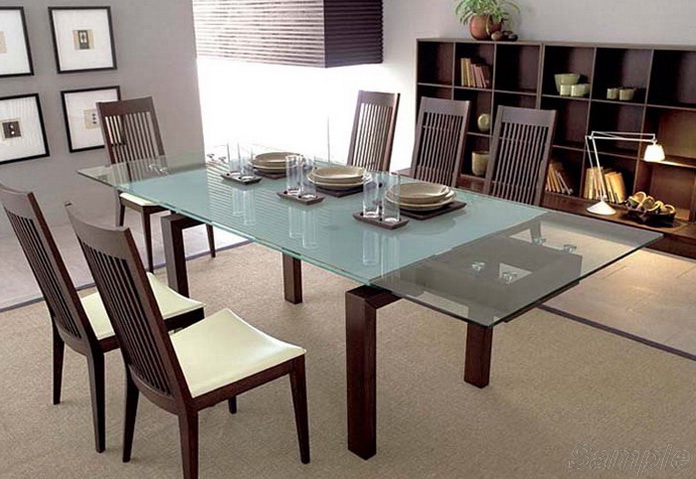
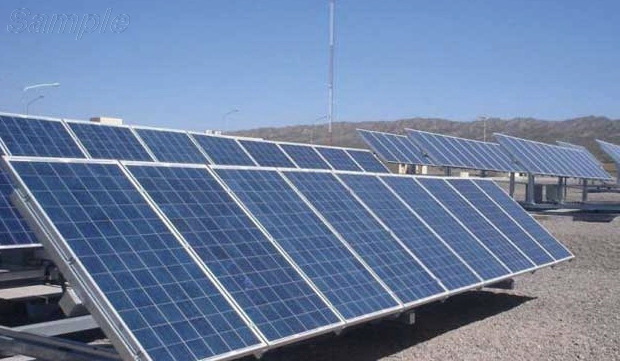
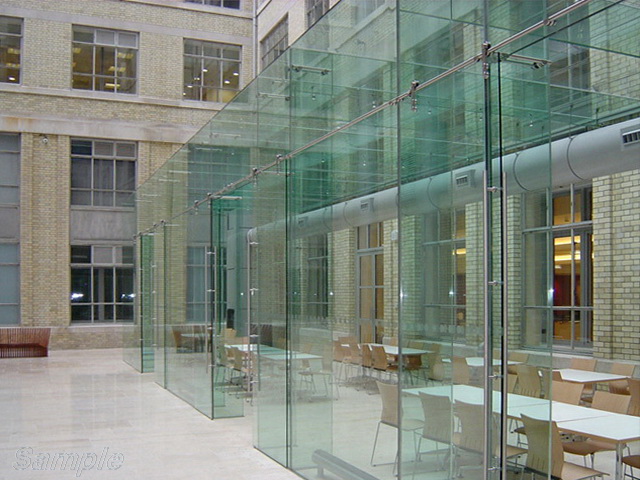
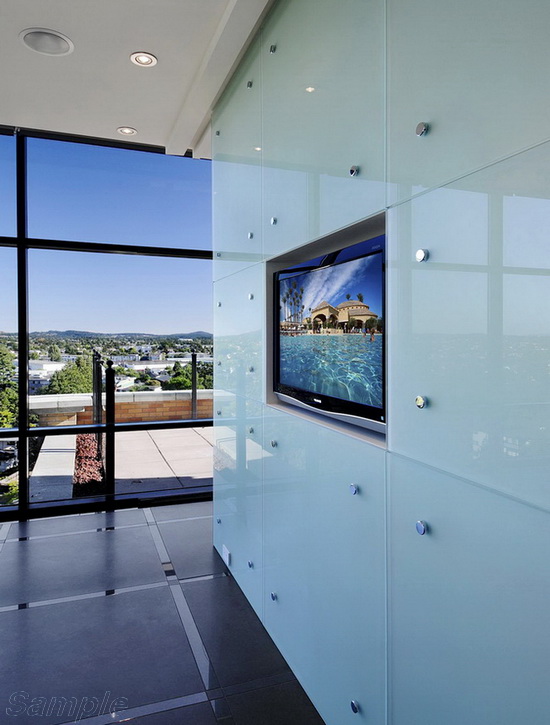
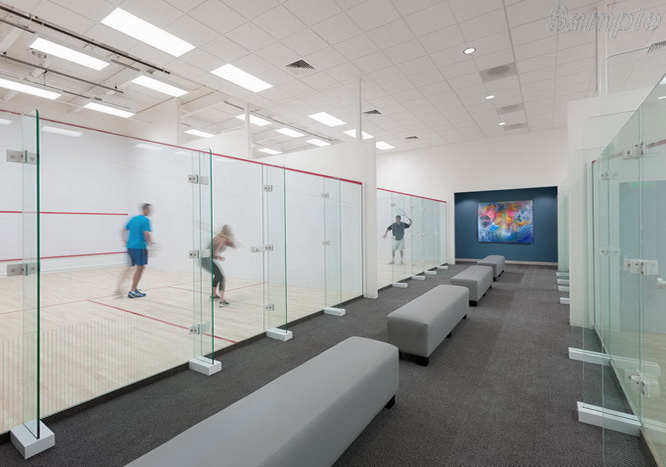
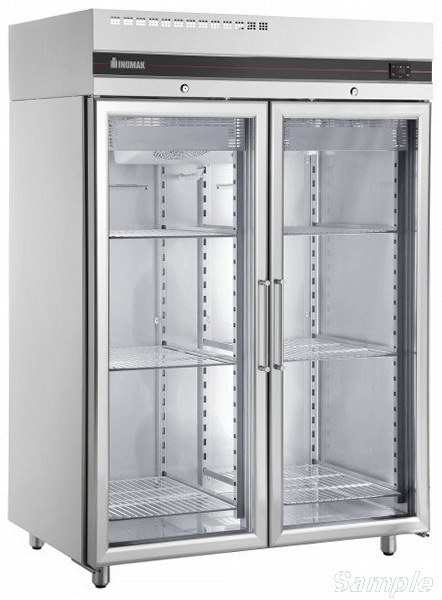
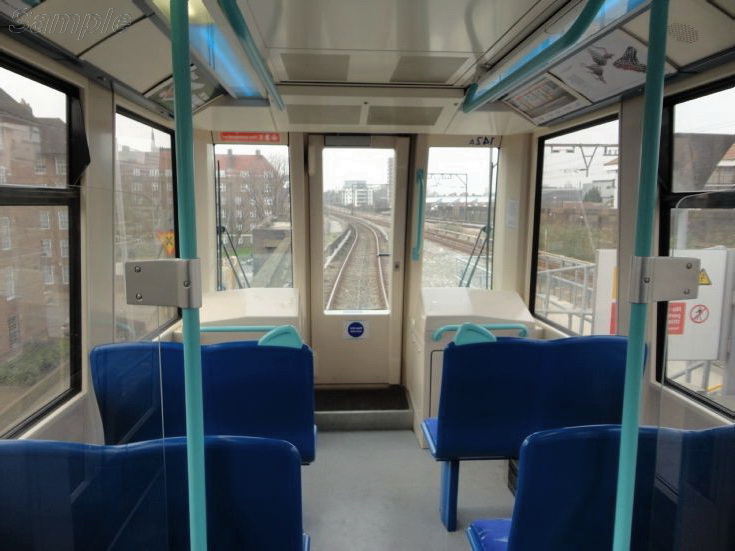
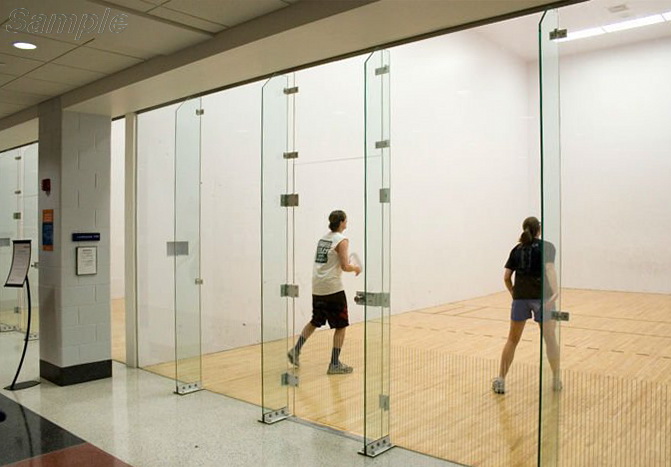
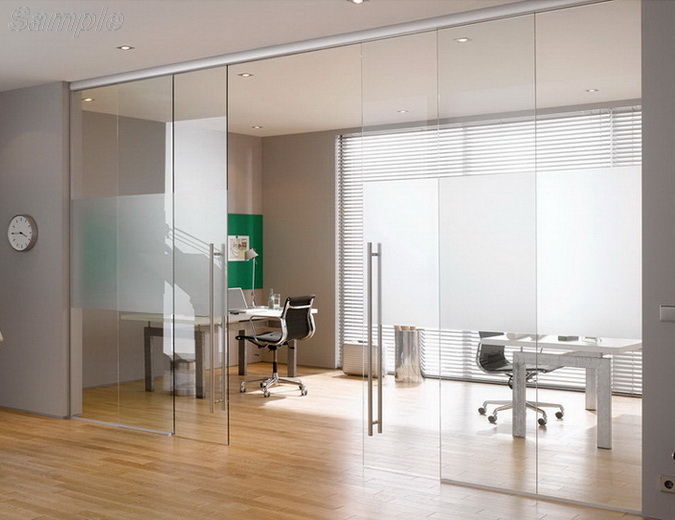
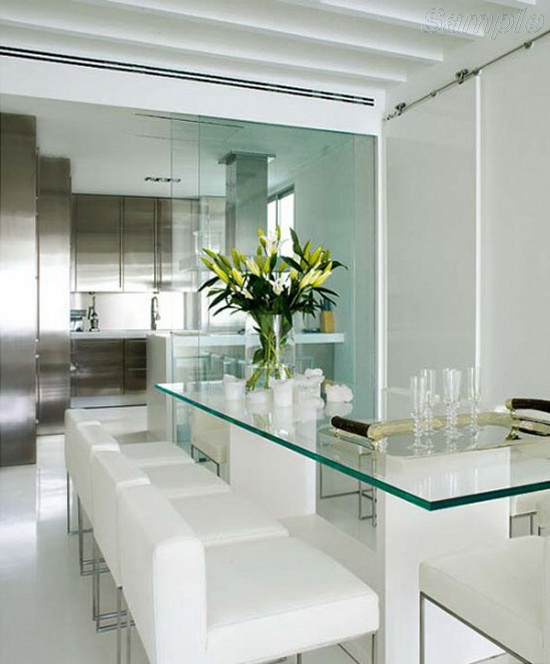
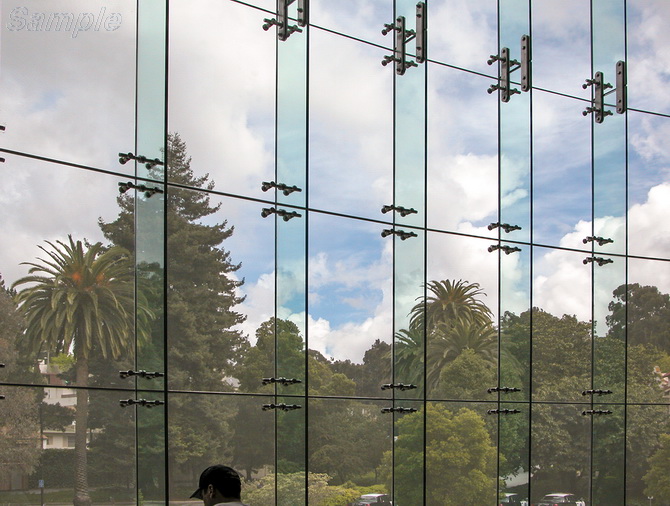
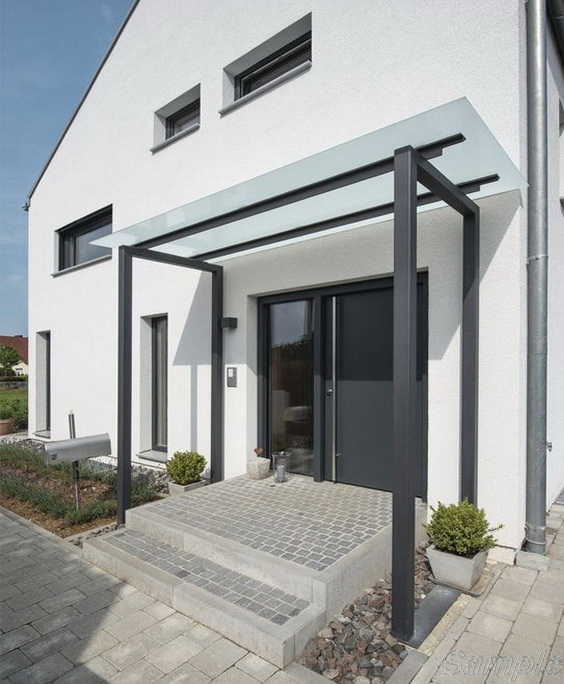
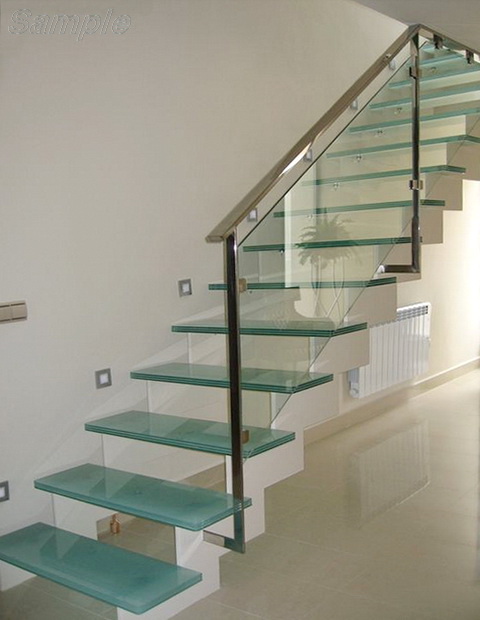
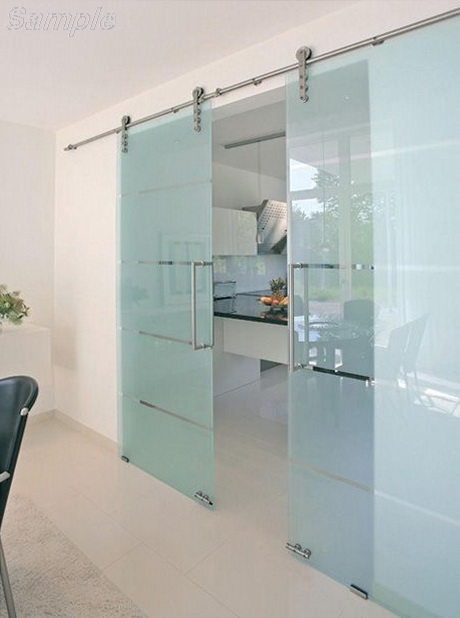
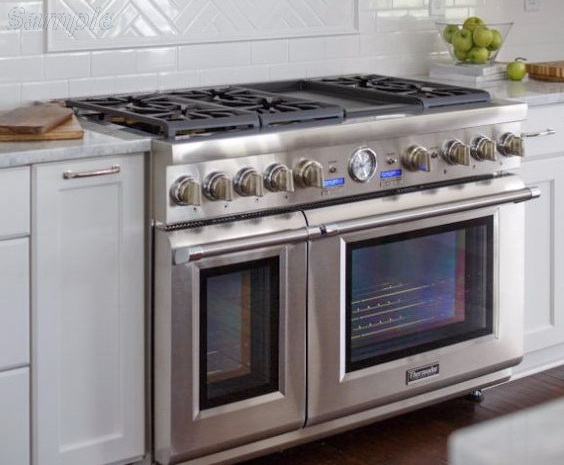
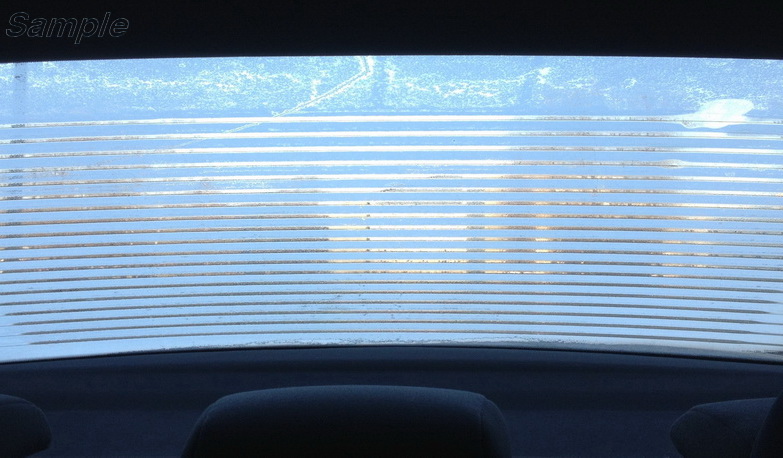
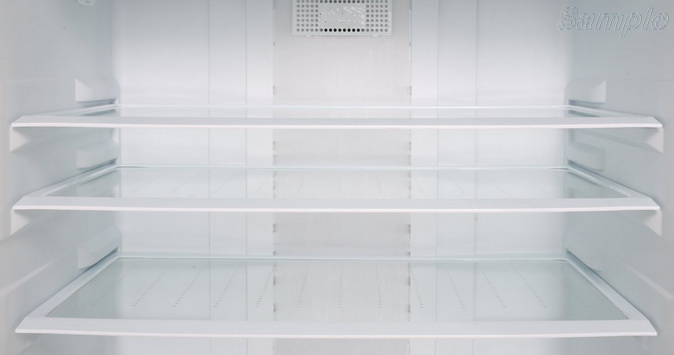
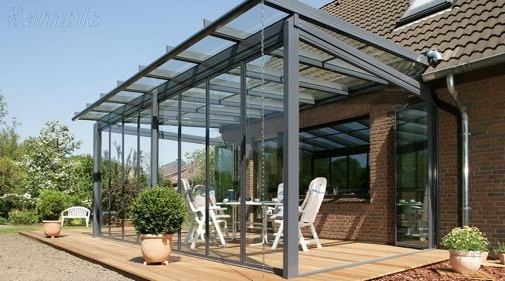
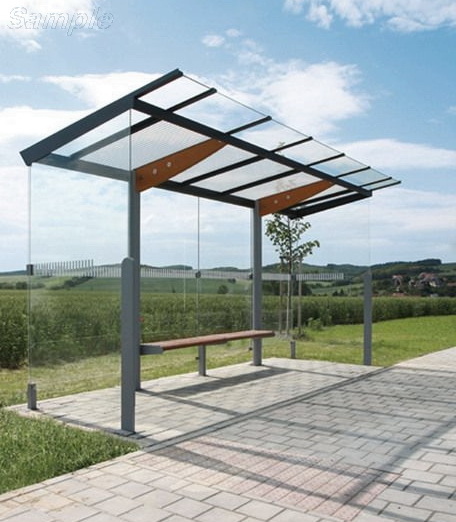
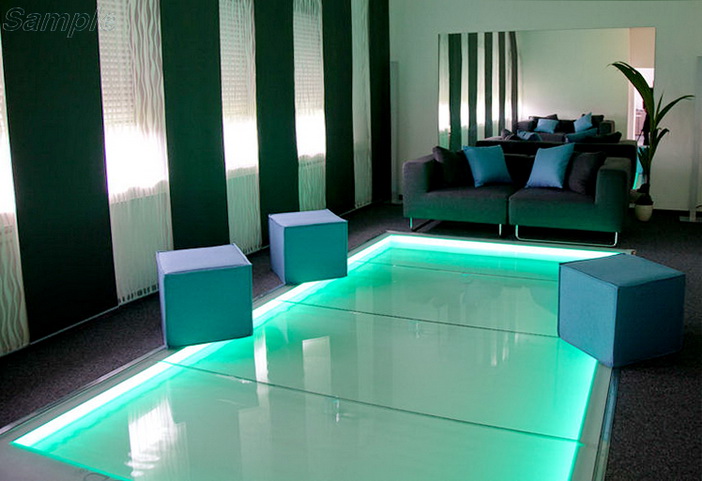
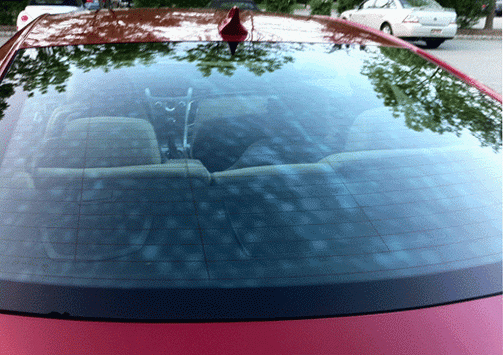
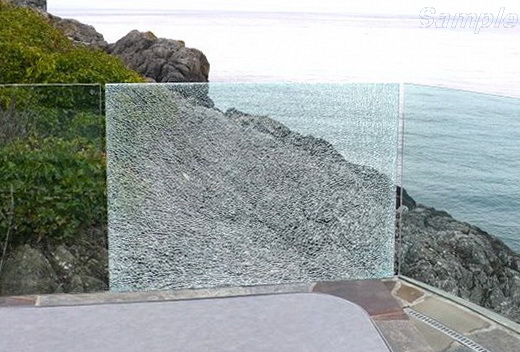
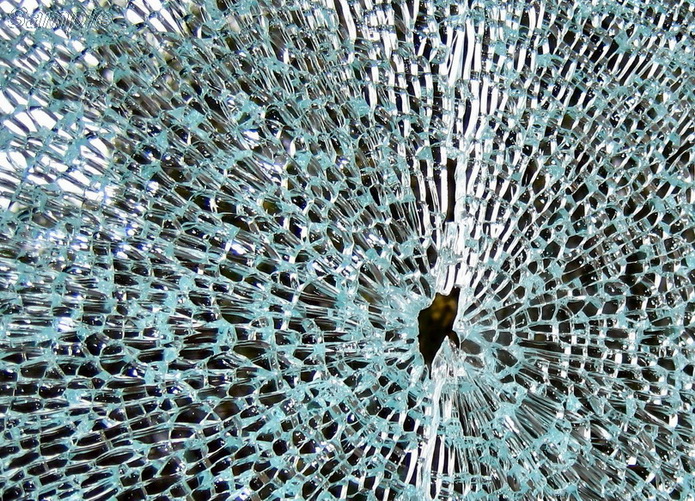
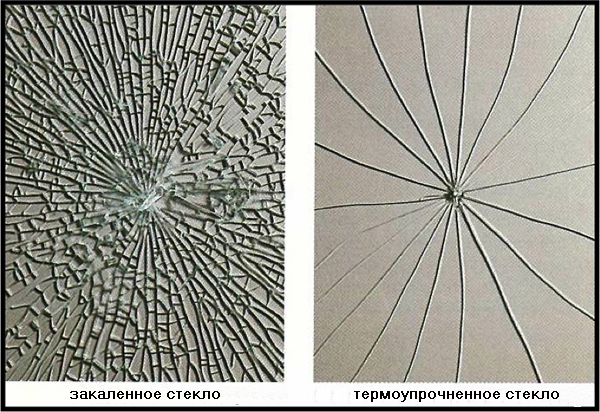
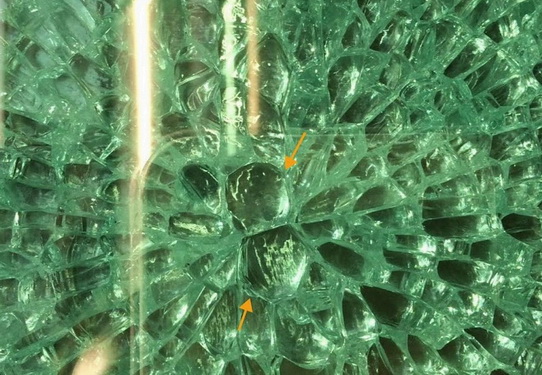
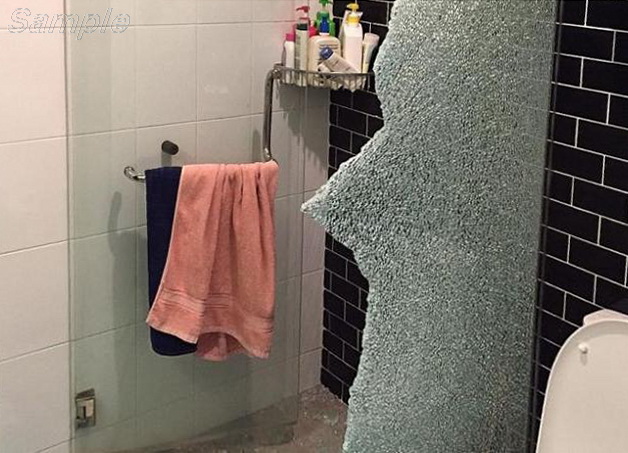
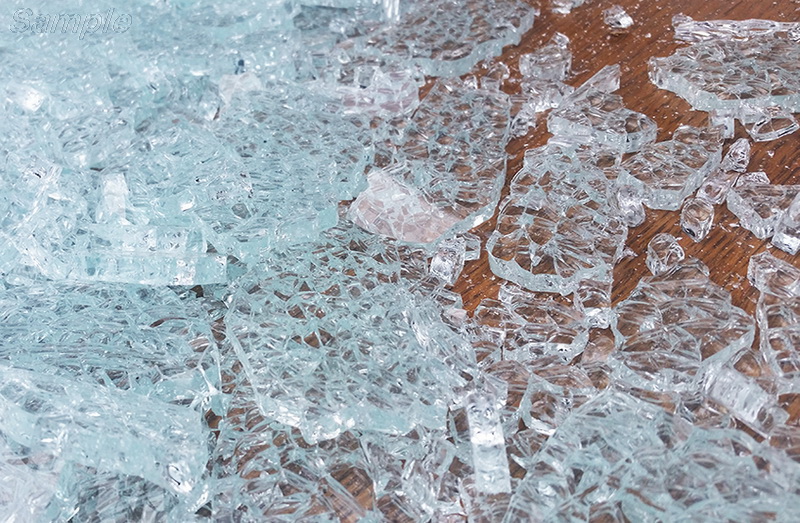
Tempered glass – a reliable and elegant construction material
- A bit of history
- Thermal glass tempering
- Advantages of thermally tempered glass
- General areas of application for tempered glass
- Thermal glass strengthening
- Heat soak test (test for accelerated aging)
- Chemical glass strengthening (chemical tempering)
- Thermally tempered glass from the “GlassPro” company
- “GlassPro” tempered glass price list and tempering services of (customer-supplied) glass from the purchaser
Attempts to manufacture tempered glass on an industrial scale began in the last decades of the 19th century. The Parisian François de la Basti is considered to be the inventor of the glass tempering process, as a result of which glass became sufficiently strong, and the method was patented in 1874. Glass products heated to a red glow were immersed in a bath with a molten mixture of fat and vegetable oil. The temperature of this mixture varied from 150 to 300 оC, and the cooling rate was adjusted in accordance with the composition of the glass, the size and shape of the product. At this time, mainly glassware, glass for lanterns and various devices were tempered.
In 1877, the German Frederick Siemens developed another process, sometimes called “glass compression,” which for the first time allowed small sheets of flat glass to be tempered. The method consisted of immersing the incandescent glass in molten paraffin heated to 200 оC, followed by cooling and squeezing the glass between the cooled metal plates. This made it possible to quickly cool the glass plate while maintaining its flatness. Experiments on glass tempering were also carried out by the German chemist Friedrich Schott, whose main works are devoted to the physicochemical properties and technologies of glass. In 1884 in Jena, he created a laboratory on the basis of which various studies of glass properties, composition, processing and tempering were carried out. In 1886, Schott founded the famous company Jenaer Glaswerk Schott und Genossen, which became famous for the production of special glasses for optics, instruments, thermometers, laboratory glassware, as well as special heat-resistant glass, which is also used in modern household appliances.
Thanks to the invention of a glass manufacturing method that involves the help of the vertical stretching of machines in 1905 by the Belgian Émile Fourcault, for the first time the production of quality sheet glass on an industrial scale was established. Glass made by the Fourcault method was the first type of flat glass, which in the 1930s began to be used by several companies to establish mass industrial production of tempered glass. Such companies included France’s Saint-Gobain and Britain’s Pilkington, which began to manufacture and sell flat tempered glass for automotive windshields. After 15 years, tempered glass would also be installed as side and rear windows in cars.
The Fourcault method was primarily used in the production of sheet glass until the end of the 20th century. It was replaced by the more progressive «float process», which was invented in the 50s by Alistair Pilkington and became the main technology of glass production worldwide. The gist of it lies in the fact that the molten glass mass, in the form of a strip with a temperature of about 1000 ° C, is pushed out of the furnace into a bath filled with molten tin. Evenly spreading over the surface of molten tin, the glass mass acquires a perfectly smooth surface. As a result of the annealing process (gradual controlled cooling), the float-glass with the smoothest parallel surfaces becomes suitable for further modern processing: automated cutting, edge processing, hardening, lamination, etc. Currently, about 90% of all tempered glass in the world is produced using float technology.
In the 20th century, glass took a stronger position in relation to other structural and building materials. It would quit being a luxury item and become a popular material in the manufacturing industry and construction.
Glass, being one of the most ancient materials, has been prized for its transparency from time immemorial, but it has always lacked strength, and the expression “fragile like glass” has become a proverb. Today, with the advent of tempered glass, we can safely say that glass has become a reliable and safe construction material. Glass destruction often starts from the surface and is caused by the development of surface micro defects. Therefore, the most common glass hardening methods are based on changing the state of its surface. This hardening is due to a decrease in the negative impact of defects on the glass surface.
There are several methods of processing glass that make it possible to increase the strength of various types of industrial glass and products from them on a production scale. At the moment, the main method for hardening glass is thermal hardening.
Thermal glass tempering (Tempered glass)
Special furnaces with complex automated control systems based on microcircuits are used in the production of tempered glass. The principle of the thermal hardening method itself is quite simple: the glass is heated in a furnace to a temperature of approximately 600 ° C, and then moved to a cooling chamber, where it is rapidly and evenly cooled by high pressure air flows. When cooled, the upper and lower surfaces of the glass cool faster than its inner layers, as a result of which compressive stresses arise in the outer layers, and tensile stresses in the inner layers. Glass is more vulnerable to bending stresses than to compressive stresses. Therefore, the compression of the surface layer of glass containing microdefects in the process of thermal hardening increases its strength to temperature extremes, bending and impact.
The mechanical strength and heat resistance of tempered glass is 5-7 times higher than that of ordinary annealed glass. When tempered glass is destroyed, its special property is manifested, which increases the degree of safety: the glass disintegrates into small safe fragments with dull edges.
Before the tempering process, glass products must be given their final dimensions and shape, since tempered glass cannot be further processed – it would be destroyed otherwise. For this reason, edging, drilling of all kinds of holes and making cutouts must precede the hardening process.
The tempering ability of glass depends on its chemical composition, thickness and the presence of additional coatings. Modern furnaces allow tempering glasses of various sizes and thicknesses, usually from 4 mm to 15 mm. Some special furnaces can temper glass in extreme thicknesses, as well as glasses with various types of functional coatings. Using the thermal hardening method, both flat and curved tempered glasses can be produced.
Systemically located iridescent dots, spots or stripes may appear on glass that has undergone a thermal hardening process under certain lighting conditions. Unfortunately this visual phenomenon, called anisotropy, will not always suit the glass facade of a building. Mechanical stress caused by the tempering process slightly changes the optical characteristics of the glass, increasing its birefringence. This phenomenon manifests itself to a greater extent in clear sunny weather and when using polarized glasses, which in this case is an advantage and will allow you to check whether you have actually purchased tempered glass.
Advantages of thermally tempered glass:
- tempered glass is 7 times stronger than normal glass and can withstand significant static loads with large deflections without breaking. This is critically important for large shop windows and external glazing elements that are subject to significant wind loads, inclined and horizontally located structures, and snow loads;
- tempered glass is highly resistant to dynamic impact loads. This is important for glass structures located in crowded places and sports facilities. In such places, glass can be exposed to various influences from careless handling, falling, being hit by objects, etc .;
- tempered glass has increased resistance to high temperatures and temperature extremes (for ordinary glass Δt = 34 ° C, for tempered glass up to Δt = 270 ° C). These properties are important for glass used for oven and fireplace doors. Functional glass facades absorb a large amount of solar energy and can heat up to high temperatures, while the individual parts of the glass element, which are covered from the sun with bead or shade, remain relatively cold. These conditions lead to the destruction of glass on the facade as a result of thermal shock. The use of tempered glass completely solves this problem.
- If it exceeds its strength limit, the broken tempered glass crumbles into small, sufficiently safe fragments;
Main areas of application for thermally tempered glass:
Tempered glass in construction
- glazing of building facades;
- glass panels for facade cladding;
- translucent roof;
- spider glazing;
- all-glass entrance doors;
- glass shop windows;
- dormer windows in the roof of the building;
- glass for telephone booths;
- glass for equipping transport stops;
- glass storefronts;
- glass overhangs and canopies;
- glass steps and stairs;
- glass railings and balustrades;
- glazing of greenhouses, winter gardens and orangeries;
- glazing of elevators;
- glazing of balconies;
- kiosk booth windows;
- glass for double-glazed windows;
- glass for sports facilities (squash halls, ice arenas, etc.);
- glazing of underwater rooms.
Tempered glass in interior
- glass interior doors;
- glass shower cabins, shower partitions and doors;
- wall-mounted glass shelves;
- fireplace and stove screens;
- glass screens for radiators;
- glass kitchen panels;
- glass floor;
- glass interior and office partitions;
- glass panels for wall cladding.
Tempered glass integrated with furniture
- shelves of cabinet furniture;
- glass tables;
- glass racks;
- glass table tops.
Tempered glass for household appliances and trading equipment
- glass in the doors of microwave ovens;
- shelves and doors in refrigerators for drinks;
- window screens of ovens;
- shelves in household refrigerators;
- walls and doors of refrigeration counters.
Tempered glass for means of transport
- side and rear windows of cars;
- insulating glass for vehicles;
- glass for working car cockpits;
- windows for ships and vessels;
- glass for metro cars, railway cars;
- glass for buses, trolleybuses, trams.
Special purpose tempered glass
- glass heated with conductive strips (for example Thermovit from Saint-Gobain Glass);
- glass for solar panels (batteries);
- safety glass in laminated structures;
- tempered glass for fire protection structures;
- anti-vandal (shock-resistant) glass;
- bulletproof glass;
- explosion-proof glass
Heat strengthening of glass (Heat-strengthened glass)
The thermal strengthening method is similar to the tempering process and consists of controlled heating and subsequent cooling of glass sheets. As with tempering, the glass is evenly heated to a temperature of about 600 ° C, but it cools more slowly. As a result of the thermal hardening process, sheet glass acquires greater mechanical and thermal strength than ordinary annealed glass. For this reason, it is often used in architectural glazing in objects with a high risk of spontaneous glass breakage due to thermal stress; for example, when glazing facades facing east or south sides. The durability of heat-resistant glass is two times higher than that of annealed glass, identical in thickness, and withstands temperature drops up to 100 ° C (tempered glass – up to 270 ° C). After the completion of the heat-strengthening process, glass cannot be processed, cut, drilled into, or subjected to deep sandblasting.
In accordance with European building codes, heat-strengthened glass is not safe and, in terms of its properties, takes the middle spot between ordinary and tempered safety glass. When shattered, heat-strengthened glass breaks into large elongated fragments, which usually allows them to remain in the frame.
Accelerated aging test (Heat soak test)
Despite careful preparation of raw materials for the manufacture of float-glass, it may contain a small amount of impurities. Usually, this does not affect the quality and consumer properties of glass, with the exception of nickel sulfide (NiS). Inclusion of this substance can manifest in a negative way during glass tempering or further operation. During the glass tempering process, the volume of NiS molecules increases, which causes additional stresses and changes its crystal structure. After a certain time, such molecules return to their original state, which can cause spontaneous cracking of tempered glass.
Heat soak test – the process of checking the glass for such inclusions before it is installed on site. Tempered glass is placed in a test oven heated to 300 ° C for 2 hours. During this time, it is easy to identify sheets with the presence of NiS: they will be destroyed (cracked) in the test oven.
Chemical glass strengthening (chemical tempering)
One of the glass processing methods which significantly increases its strength is chemical strengthening. The glass is immersed in a container with potassium nitrate heated to a temperature of 450 ° C. Sodium ions in the surface layer of glass replace potassium ions contained in the solution. Ion exchange creates surface tension and hardens the glass.
Chemical tempered glass is used in:
- aviation and the space industry;
- the military field (guidance devices);
- windshields of yachts and boats;
- lighting devices in watch cases;
- mobile phones and tablets.
Advantages of chemical glass strengthening:
- Provides the ability of tempering glass of small volume and thickness;
- After the tempering process, the glass can undergo further processing;
- Provides strengthening of glass products of complex geometry (including glass bent in several planes);
- suitable for windshields (being a part of triplex, the damaged glass remains transparent without forming a fine turbid mesh, so the driver can safely reach a repair shop).
Disadvantages of chemical glass tempering:
- Process takes significantly longer than thermal tempering;
- upon reaching the threshold of destruction, unlike thermally tempered glass, it breaks up into large sharp fragments. Therefore, chemically tempered glass cannot be considered safe;
- the technological process is environmentally unsafe.
Thermally tempered glass from the “GlassPro” company
The company “GlassPro” offers glass, processed and tempered in our own production, as well as provides services for tempering customer-supplied glass.
Ownership of the Certificate of Conformity for tempered building glass of the following thicknesses: 4 mm, 5 mm, 6 mm, 8 mm, 10 mm, 12 mm, 15 mm, 19 mm, meeting the requirements of DSTU B V.2.7-110-2001 (GOST 30698-2000)..
Our own production with a full cycle of glass processing:
- Preparation of computer blueprints of products for the project;
- Glass marking based on blueprints;
- Cutting glass on an automated CNC line;
- Drilling holes and making cutouts of varying complexity;
- Grinding and polishing of straight and curved edges;
- Automated glass washing;
- Glass tempering procedure;
- Production of laminated glass using tempered glass;
- Quality control at all stages of production;
- Glass packaging;
- Delivery of glass to a facility in Ukraine.
Technical capabilities of the glass tempering furnace of the “GlassPro” company:
- Maximum size of tempered glass: 3600 × 2440 mm;
- Minimum size of tempered glass: 300 × 100 mm;
- Glass thickness: from 4 mm to 19 mm;
- Possibility of thermal glass strengthening;
- Tempering of transparent and extra-transparent glass;
- Tempering of frosted and patterned glass;
- Tempering of mass tinted glass;
- Tempering glass with various types of sun-reflective and low-emission coatings.
Computer control allows you to select the most suitable tempering process dimensions for each type of glass and provides accurate control of temperature, stability and repeatability of the process. The control system allows you to control the temperature in 88 zones, on which the heating chamber is evenly distributed.
Our furnace is equipped with an additional air convection system in the heating chamber, which improves the quality of tempering glass of thin denominations, as well as glass with various types of functional coatings. Modern equipment and GlassPro’s highly trained operators allow us to create tempered glass of the highest quality that meets all domestic and international regulations.
“GlassPro”tempered glass and customer glass (supplied by the client) tempering services price list